Nacre is the natural composite found in the shells of mollusks, such as oysters and abalone. It is composed primarily of aragonite crystals, the formation and growth of which are biologically controlled by thin layers of chitin. This microscale composite structure makes nacre stiff and tough, also producing nacre’s iridescent properties.

Detailed study of nacre’s crystals reveals an orthorhombic system; slight variations in cell orientation and growth rate are responsible for the overall 3D form and fractal-like patterns of natural shells. These patterns and irregularities serve as set of design parameters for growing digital nacres, with key variables including initial point seeding, shape of cells, and growth rate.
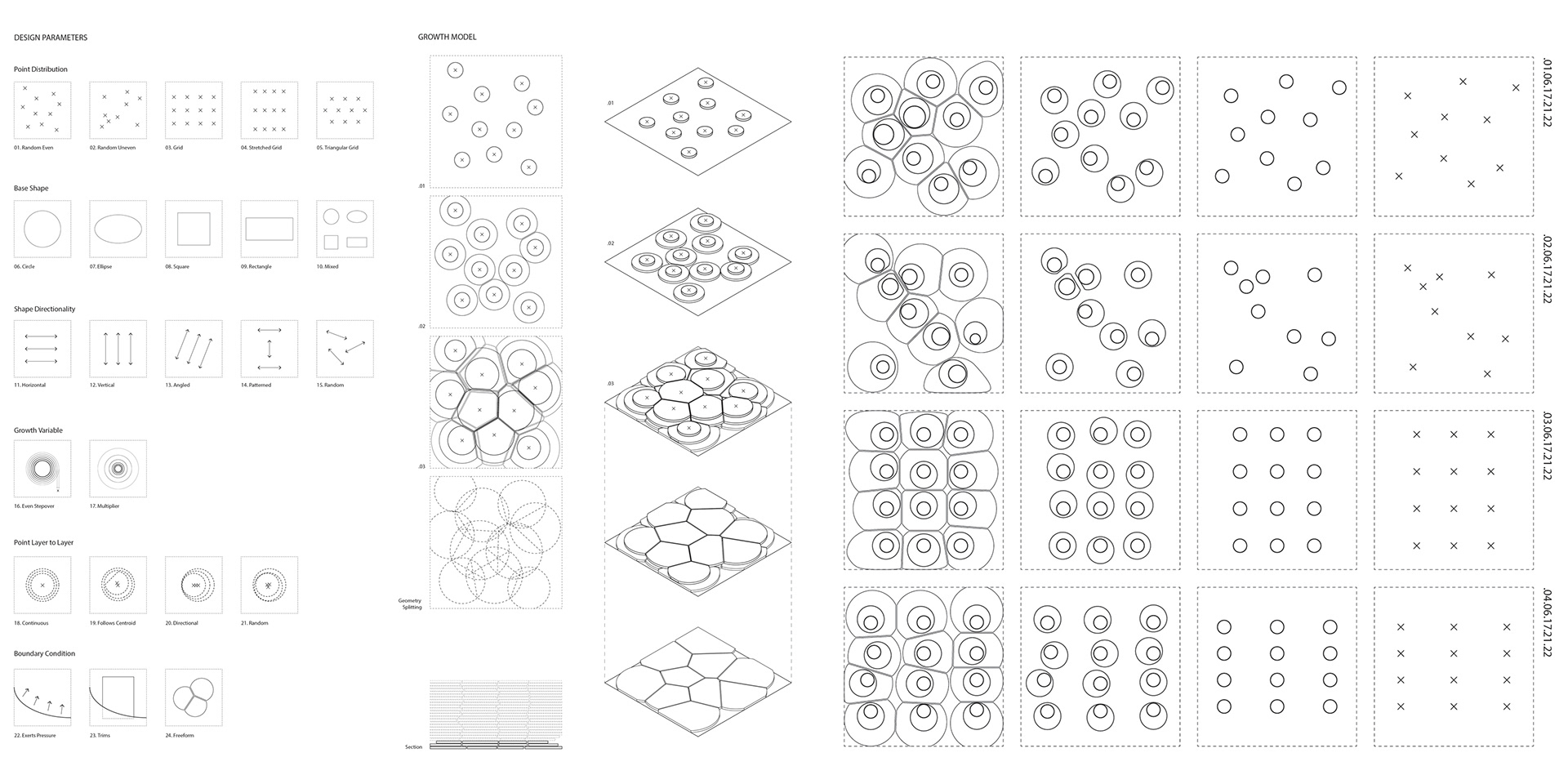
Initial material tests aimed to produce a biocompatible material suitable for robotic extrusion by combining one or more of:
amorphous calcium carbonate (CaCO3), chitin, chitosan (deacetylated chitin), silk fibroin, acetic acid, hydrochloric acid, water

It was found that a bioplaster material composed of calcium carbonate, chitosan, acid and water would curl and exhibit self-lift as it dried; this lead to a nacre-derived fabrication system for exploring transformations between 2D surface and 3D shell.
To accurately fabricate digital nacres out of the bioplaster material, several robotic setups were tested, with the final design consisting of an ABB IRB120 robot with a custom 6th axis rotation-driven push extruder as its end effector.
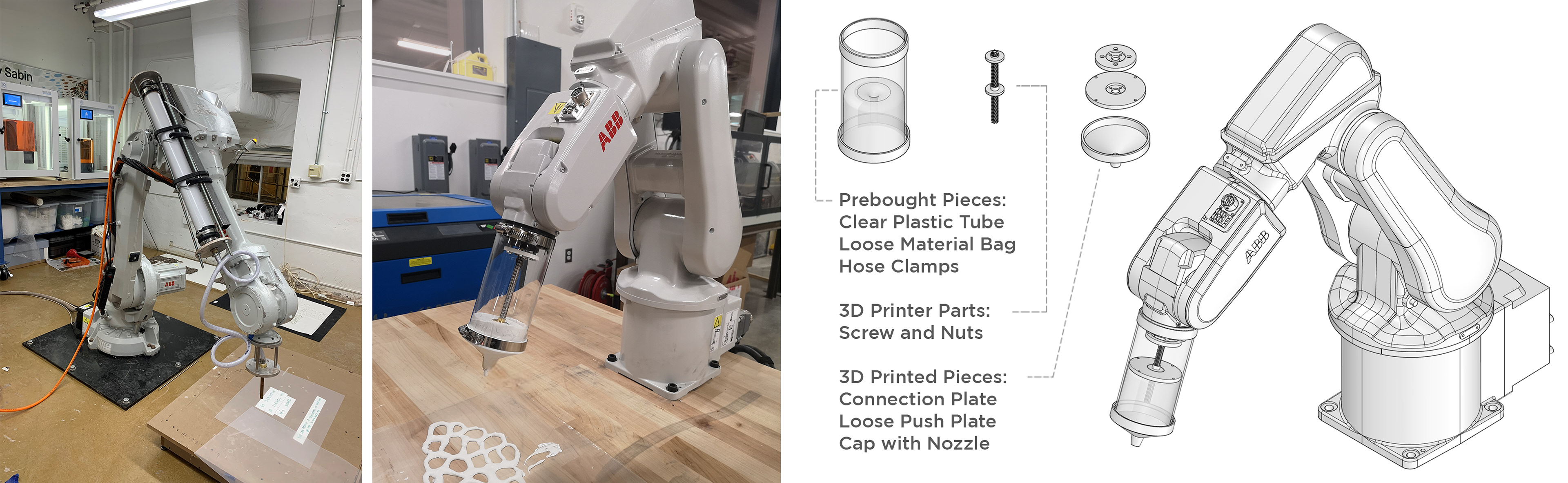
A series of prints were produced to investigate the effect of changes in 2D surface topology on formal/spatial properties of the resulting 3D shells. This process of 2D to 3D transformation presents an architectural opportunity for emergent form finding.
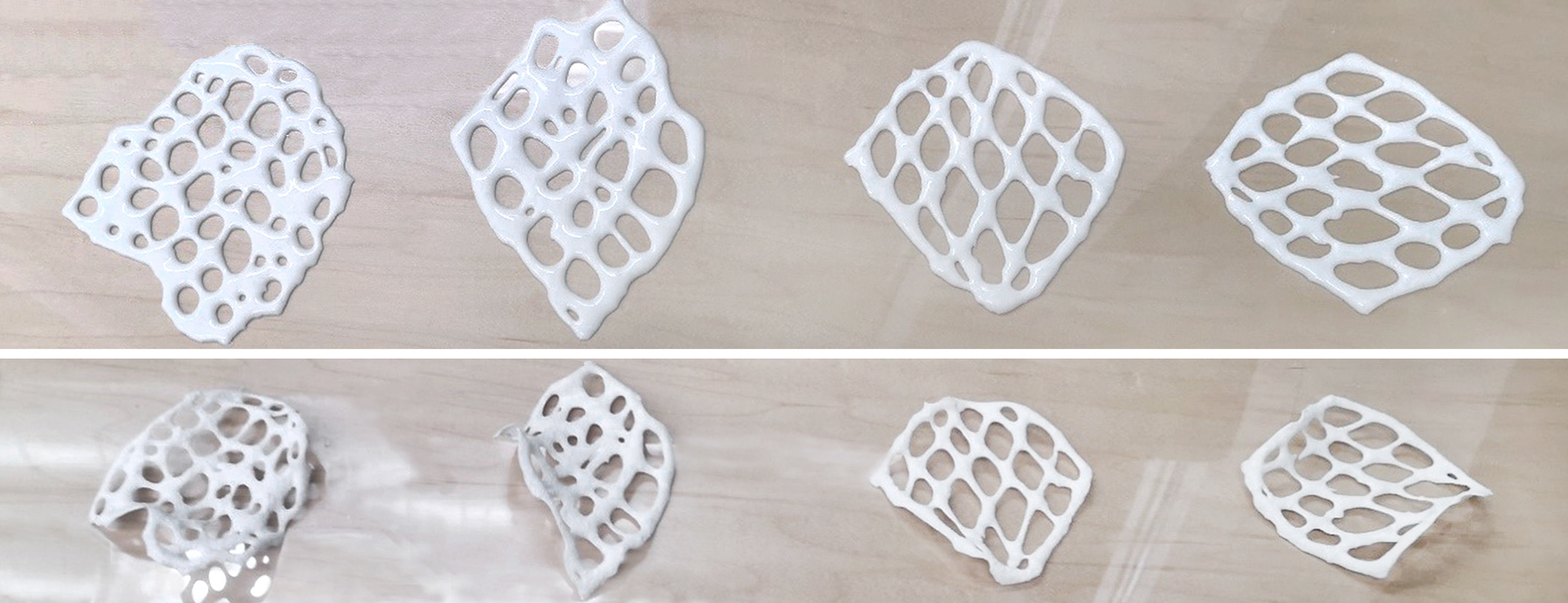
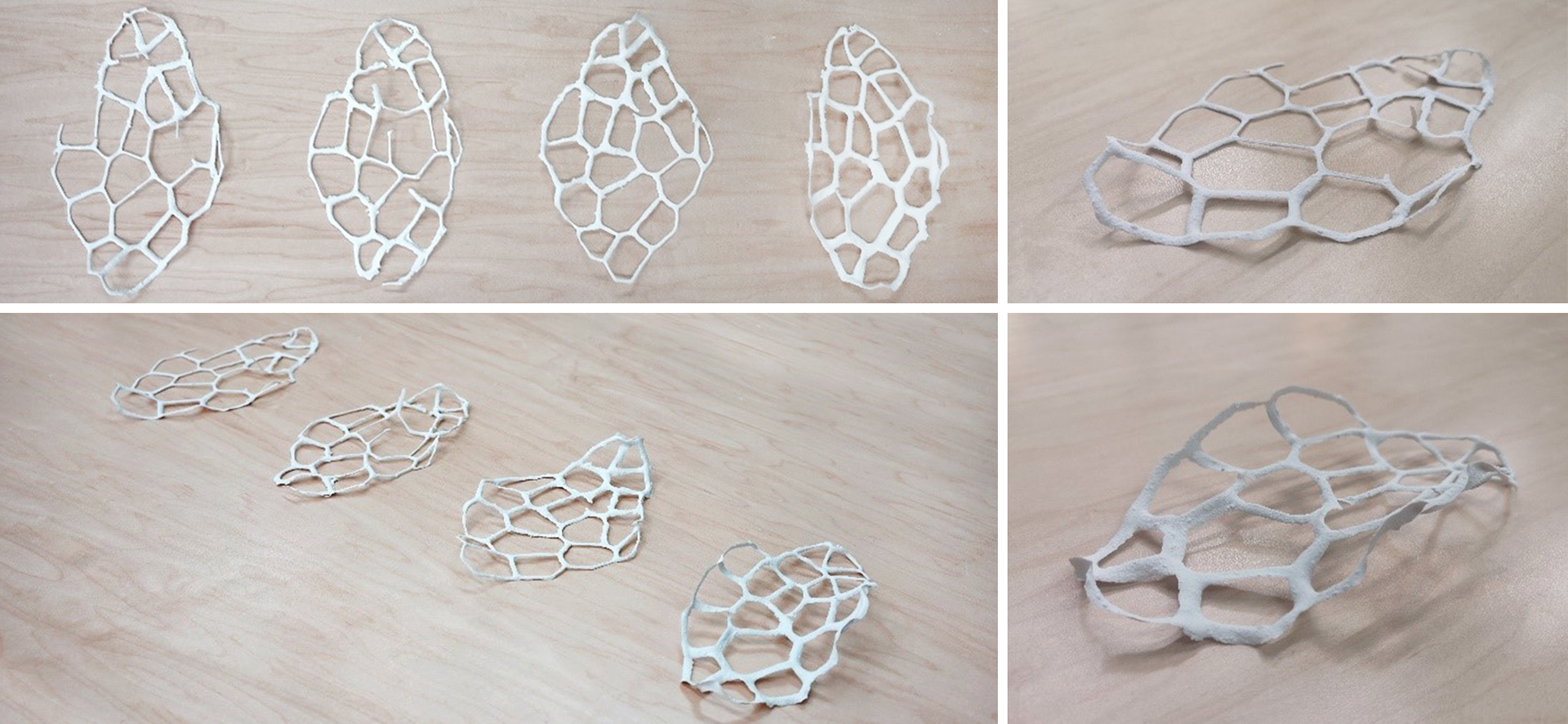
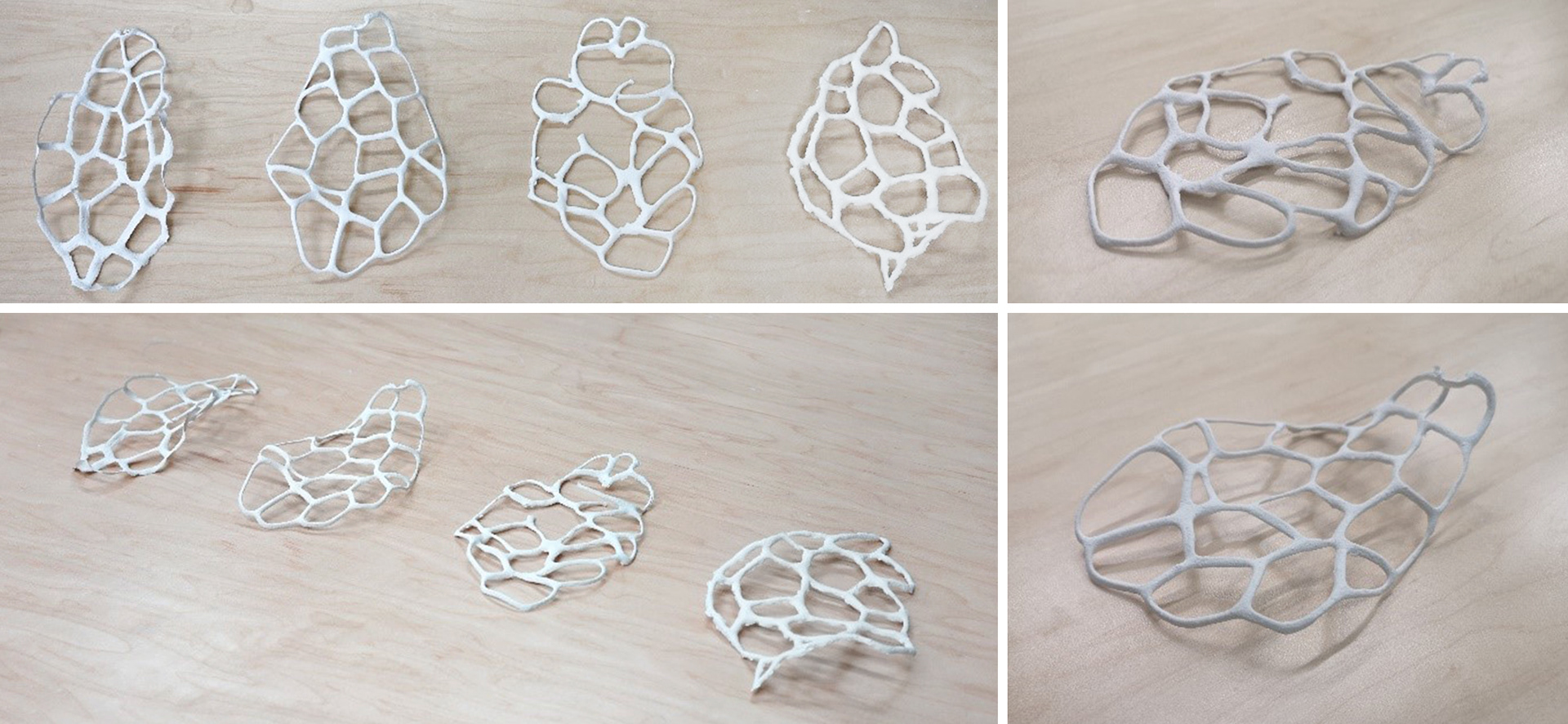